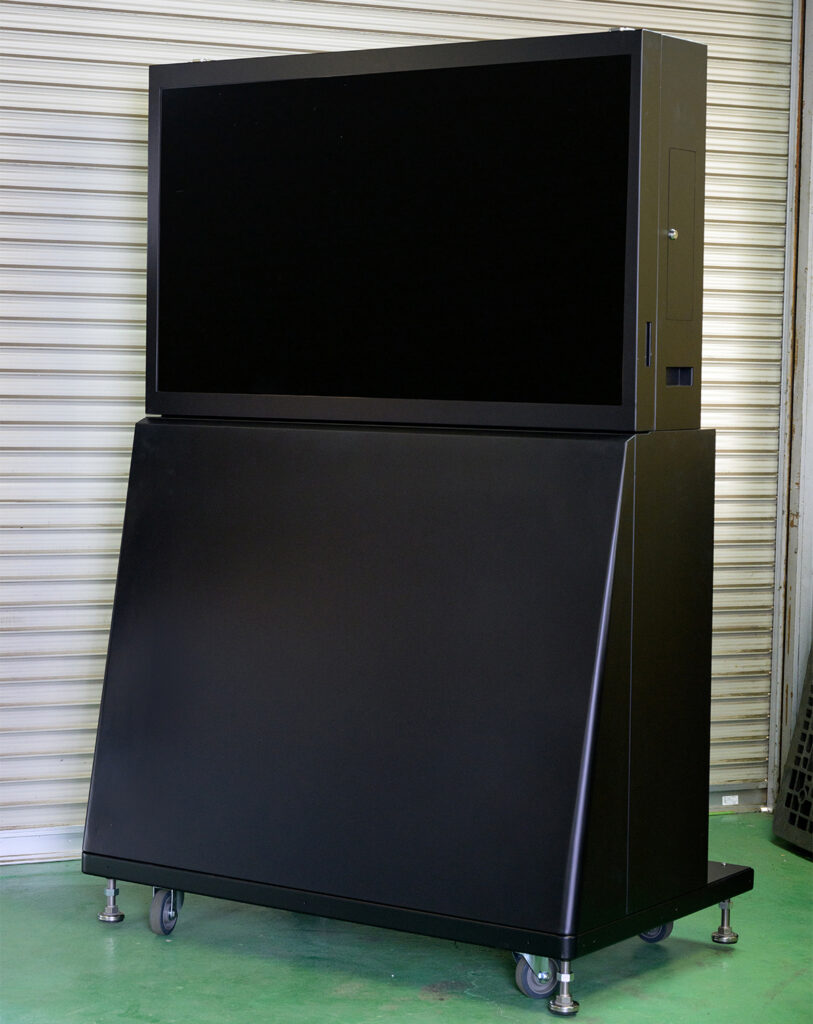
板金設計では、図面上では問題ないように見えても、製造現場で思わぬトラブルが発生することがあります。ここでは、よくある設計トラブルとその予防策をQ&A形式で紹介します。
Q1:曲げ加工後に穴位置がずれてしまうのはなぜ?
A1:展開図における伸び代の計算ミスが原因です。板厚、R、曲げ角度に応じた補正値を使用し、展開寸法を正しく算出しましょう。設計段階でCAM担当や加工現場と連携することも重要です。
Q2:溶接による歪みでフレームが組み合わない
A2:溶接順序・溶接量・仮付けの有無によって、熱歪みが蓄積し、精度にズレが生じることがあります。設計段階で溶接部の配置と冶具の活用方法を事前に検討しましょう。
Q3:外観面にスパッタや焼け跡が残っていた
A3:図面で外観面/非外観面の指示が明記されていないと、現場判断に任されてしまい、仕上げ品質が不安定になります。部位ごとに仕上げ等級や処理の有無を記載するようにしましょう。
Q4:ネジ穴と部品の位置が合わない
A4:寸法公差を厳しく設定しすぎたか、またはクリアランスが不足していた可能性があります。部品間の累積公差を考慮し、穴位置には適切な余裕を設けるよう設計してください。
Q5:検査が困難で製品の合否判断に時間がかかる
A5:寸法基準が検査具で測定できない場所にある、または基準点が不明確な設計になっていることが原因です。検査性を考慮した寸法配置や、測定基準の明記が有効です。
これらの問題は、事前に現場とすり合わせを行うことで多くが予防可能です。「現場との対話」と「過去の失敗から学ぶ姿勢」が、設計の成熟度を高め、再発防止につながります。図面の一つひとつが、実際に形になることを意識し、机上の理論だけに留まらない「使える設計」を目指しましょう。