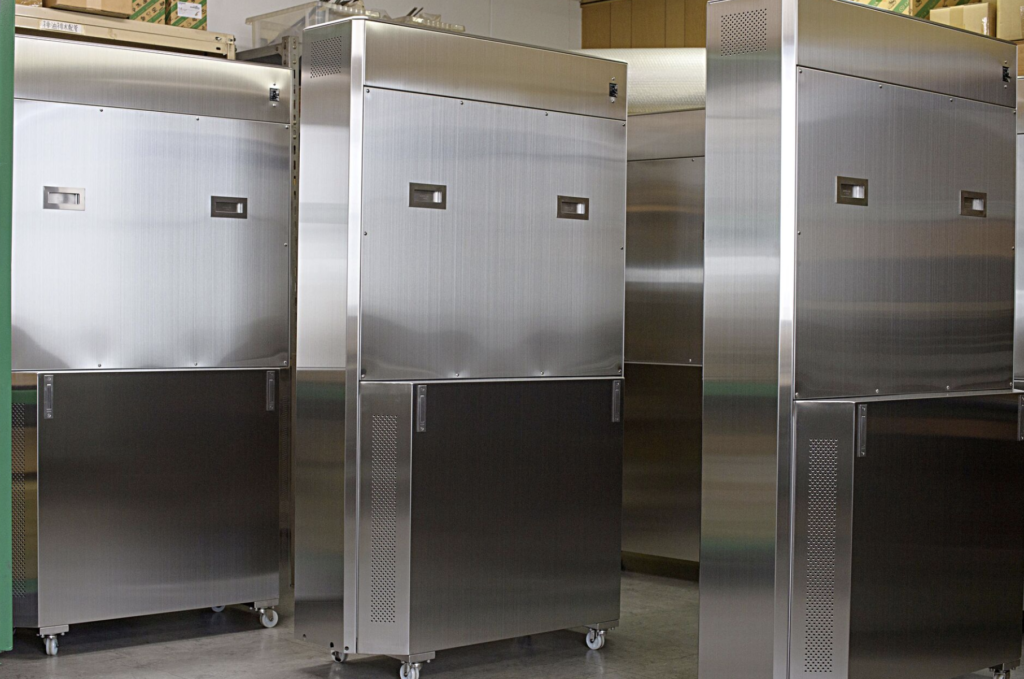
板金部品の組立精度は、単品部品の寸法精度だけでなく、組立時の位置決め、接合方法、治具設計に大きく左右されます。設計段階での組立性配慮が不十分だと、現場での組立ズレや精度不良の原因になります。
まず、組立時に重要なのは「基準面の明確化」です。どこを基準にして部品を組み立てるかを設計図で明示し、各部品の取り付け面・位置決めピン穴・止め具の位置などを論理的に整合させる必要があります。基準が不明確なままだと、製造現場での仮合わせややり直しが発生し、工数増につながります。
また、位置決め構造の工夫も有効です。位置決め用の凸凹やピン、スロット形状を取り入れることで、誰でも再現性の高い組立が可能になります。特に溶接構造では、仮付けでのズレが後工程に影響するため、初期位置合わせの精度確保が重要です。
さらに、冶具設計も設計者の配慮ポイントです。量産を前提とした設計では、専用冶具を用いた組立を想定し、部品の自立性や固定性を考慮した設計が求められます。治具が無くても位置が決まる構造を考えることで、製造現場の負担を減らし、組立時間を短縮することができます。
溶接、カシメ、ボルト接合など、組立方法ごとに許容公差や必要精度は異なります。接合面の隙間、平行度、直角度などに配慮した構造とすることで、後加工や手直しの手間を削減できます。
また、組立性の良い設計には「作業性」と「検査性」の視点も不可欠です。工具が入りやすい配置、測定しやすい基準、メンテナンス性の確保など、製造・検査・保守の各工程での使いやすさを意識することで、製品の信頼性が向上します。
設計者が単品図だけでなく、組立全体を見通した設計を行うことで、トータルでの製造精度と効率が向上します。部品単体の美しさだけでなく、「組み上がったときの精度と安定性」を意識することが、高品質な製品づくりの鍵です。