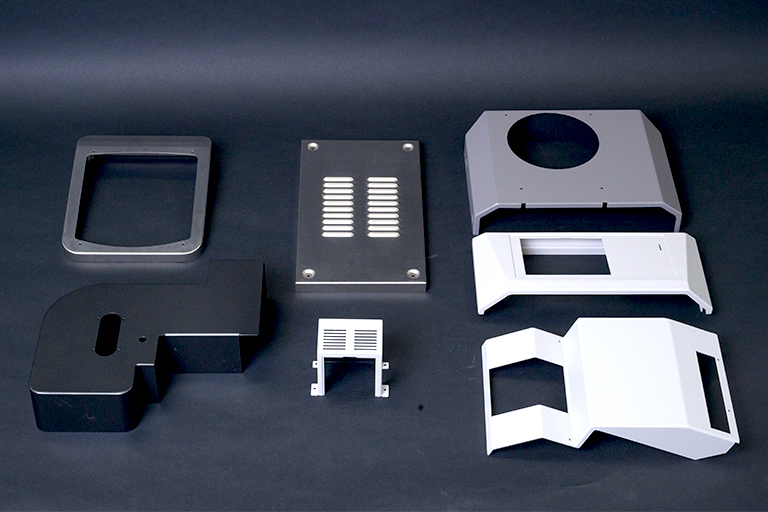
設計者と製造現場の間には、考え方や用語、目的意識の違いからくる「設計と現場のギャップ」が存在します。図面上では理想的に見える設計も、現場での加工・組立・検査の実作業に落とし込むと、想定外の手間や不具合が発生することがあります。このギャップを埋めるためには、設計者が製造現場の目線で設計を見直す姿勢が不可欠です。
まず設計時に心がけたいのは、「加工性」「組立性」「検査性」を三位一体で考えることです。たとえば、設計図面に表記されている寸法や公差が、実際に測定可能な位置にあるか、検査具が届くスペースがあるかといった視点は、図面作成時に見落とされがちです。現場では「工具が入らない」「部品が立たない」「溶接の姿勢がとれない」など、日々の作業で直面する問題が多く、これらに配慮した設計が求められます。
また、作業ミスの発生しやすい工程や、作業員の負担が大きい構造を避ける工夫も重要です。たとえば、仮付け位置が不明確な溶接部品や、左右対称でないフレーム構造は、作業者がその都度位置調整を強いられるため、組立時間が増加し、品質にもばらつきが生じやすくなります。これに対し、ピンや段付き構造、位置決め穴などを用いた設計であれば、再現性と作業性が大きく向上します。
設計と現場のギャップを減らすには、製造担当者との対話が欠かせません。設計レビューの場に現場担当者を招き、図面の意図や背景を説明しながら、加工しにくい部分や過去のトラブル事例などを共有することで、改善のヒントが得られます。また、実際の製品加工現場を定期的に見学・体験することで、作業者の立場から設計を見直す力も養われます。
さらに、設計と現場をつなぐツールとして、「設計意図書」や「製造ノート」などの補足資料を活用するのも効果的です。図面には記載しきれない情報や製造上の注意点、特に優先したい仕様などを文章で補足することで、現場との認識ズレを防ぐことができます。
製造現場に信頼される設計者とは、理論だけでなく現場感覚を持ち、対話と協働を重ねながら最適な設計を実現できる人物です。現場目線を取り入れた設計は、単なる製品仕様の実現にとどまらず、品質・生産性・安全性すべてを向上させる設計品質そのものを高める力となります。