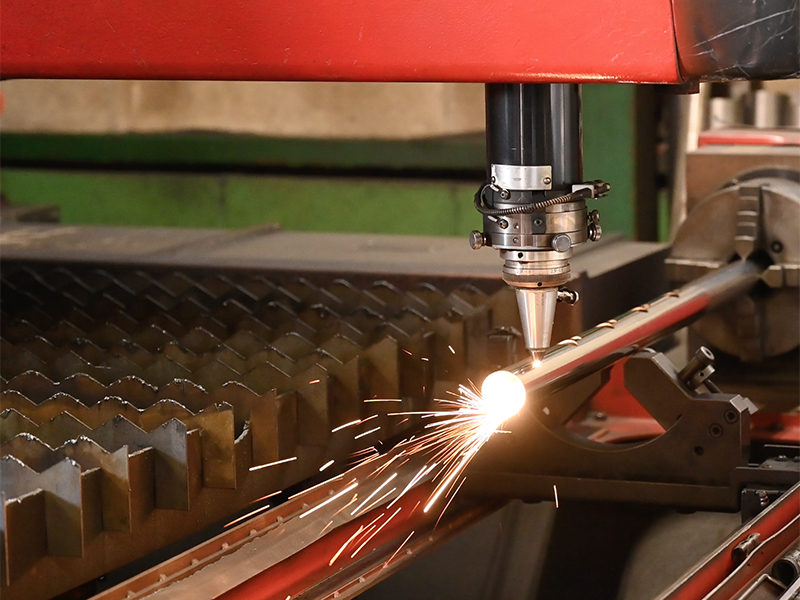
レーザー加工は、板金加工における切断工程で最も広く利用されている技術の一つです。高出力のレーザー光を利用して金属板を溶融・気化させ、極めて精密な切断が可能であることから、複雑な形状や小ロット生産にも適しています。しかし、万能ではなく、材料や板厚、形状によって限界が存在します。これを理解して設計することが、量産性・品質・コスト面で非常に重要です。
まず、レーザー加工に適した材料には、SPCC、SUS304、A5052などが挙げられます。特に、ステンレスやアルミのような非鉄金属では、反射率が高いため高出力のレーザーが必要になることがあり、加工条件の調整が求められます。加工可能な板厚は、一般的なファイバーレーザーであれば鉄でt0.5〜t12程度が目安です。これを超える厚みでは、切断面が荒れる、切断速度が著しく低下するなどの問題が生じやすくなります。
形状面では、極端に細いスリットや微細な穴、連続した狭ピッチ形状などは熱影響やレーザービームの焦点径の影響を受けやすく、変形やバリの原因になります。また、角の部分の急激な方向転換や極小半径の加工は、切断品質を損なう要因となります。こうした制限を理解し、設計段階で加工限界を超えない図面作成を行うことが重要です。
また、レーザー加工には「加工順序」や「焼け」「スパッタ」など、外観品質に関わる要素もあります。とくに外装品の場合、レーザー起点のマーキングや溶融痕が見えることを嫌うケースも多く、加工向き(裏面からの切断)や追加工(仕上げ研磨)を前提とした設計配慮が求められます。
レーザー加工は金型が不要なため、初期コストが抑えられ、設計変更にも柔軟に対応できます。その一方で、加工コストは切断距離と加工時間に大きく依存します。よって、設計者は不必要な切断距離を避け、連続性のあるシンプルな形状を心がけることでコストダウンにも貢献できます。
結論として、レーザー加工の強みと限界を理解した上で、最適な形状・材料・加工指示を設計段階で盛り込むことが、品質向上と生産性確保の鍵となります。加工業者との密な連携によって、最適解を見出す姿勢が求められます。