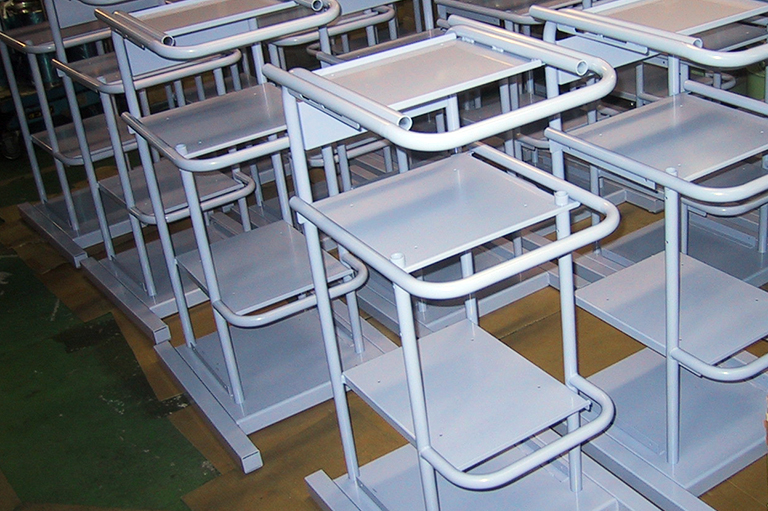
板金加工において、コストは設計段階で大きく左右されます。材料費や加工費だけでなく、組立工数や仕上げ処理などを含めた総合的なコストを意識した設計を行うことで、品質を損なわずにコストを抑えることが可能です。
まず最初に考えるべきは「加工しやすい形状」にすることです。たとえば、不要に複雑な曲げ、急なR形状、深絞りのような特殊形状は、専用金型が必要になる場合もあり、コスト増の原因となります。単純な曲げ構造や、既存の金型で対応可能な形状に設計することで、加工工数と金型費を削減できます。
次に「部品点数の削減」も有効な手段です。複数の部品に分かれていた構成を一体化することで、溶接や組立工数を削減できる場合があります。たとえば、左右対称の部品を1つの型で共通化する、あるいはボルト止めから板金加工による一体成形に変更するなど、部品構成の見直しがコストダウンに直結します。
材料歩留まりの最適化も忘れてはなりません。標準板サイズ(例:1219×2438mmや1000×2000mm)を基に展開寸法を設計することで、無駄な端材を減らし、材料費を大きく圧縮できます。材料選定時には、必要以上に高級な材料や厚板を選ばないよう注意し、機能とコストのバランスを取ることが求められます。
さらに、仕上げ処理や塗装の省略も検討の余地があります。見えない部分に研磨や塗装を施す必要があるか、製品仕様として本当に求められているかを設計段階で見極めることで、後工程の削減につながります。
また、設計段階で「標準部品」「共通部品」を採用することも有効です。特注のネジやブラケットを避け、既製品で代用することで、調達コストや在庫管理の効率が向上します。加工工程を統一・簡素化することで、外注先や自社工場での製造負荷を軽減できます。
最後に、設計と製造の現場が密接に連携することが、最も効果的なコストダウン手段です。加工現場や購買担当者と早期に情報を共有し、「この構造なら加工が簡単」「この形状は時間がかかる」といったフィードバックを設計に反映することで、実現性の高い製品設計が可能になります。
板金加工のコストダウンは、単なる価格交渉ではなく、設計の工夫と現場との協働によって達成されます。長期的に見て無理のない形でコスト競争力を高めるためにも、設計者の段階でできる工夫を積み重ねることが重要です。