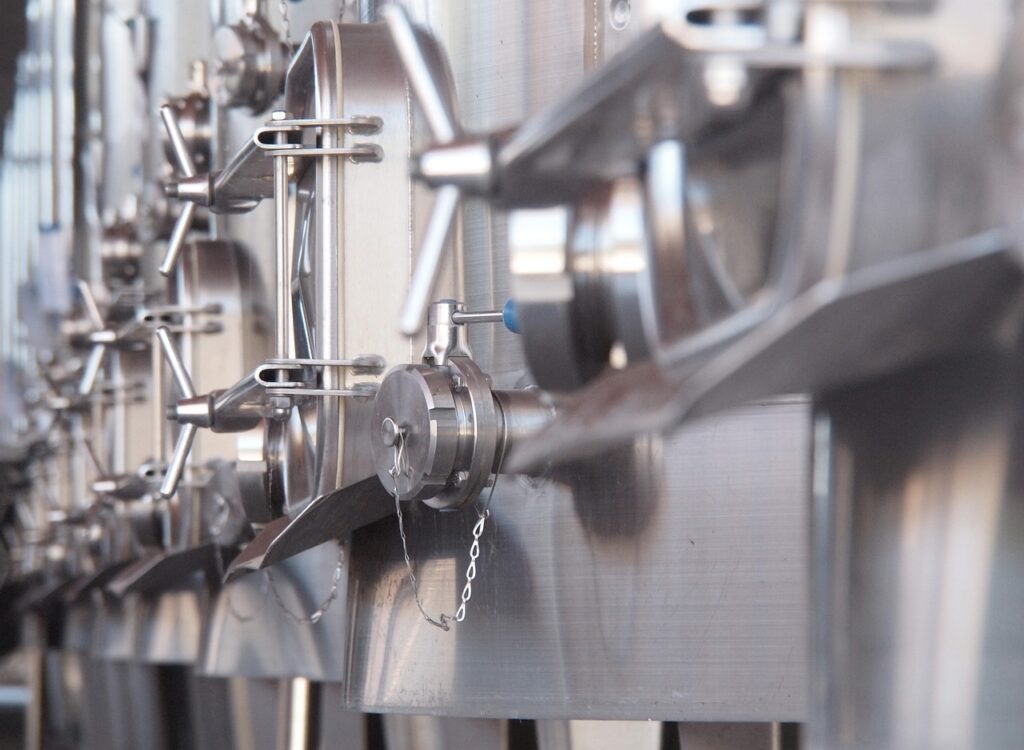
ステンレス板厚選定のチェックリストとその具体例
板厚選定においては、具体的な基準とポイントを押さえることで、製品性能とコストのバランスを効率的に図ることが可能。以下は、板厚選定時に考慮すべき要素をまとめたチェックリストと、その適用例。
チェックリスト
- 使用環境
- 屋内/屋外、腐食性の高い環境の有無
- 化学物質や高温への耐性が求められるか
- 必要な強度
- 外部からの荷重や衝撃の程度
- 長期使用における耐久性の必要性
- 加工方法
- 切断、曲げ、溶接の手法とそれに適した板厚
- コスト制約
- 素材費、加工費、輸送費のトータルコスト
- 製品重量の制限
- 軽量化が求められる用途かどうか
適用例
- 食品業界向け厨房設備
耐腐食性と衛生面の観点から2mm程度の板厚を採用。加工のしやすさとコストパフォーマンスを両立するため、レーザー切断を利用。 - 屋外設置の医療機器カバー
腐食や風雨に耐えるため3mm以上の板厚を採用。強度解析に基づき、荷重が集中する部位のみ4mm厚を追加。
板厚と加工方法の関係を明確に示した表
以下は、主な加工方法と推奨板厚をまとめた表。これにより、どの加工が板厚と最も相性が良いかを一目で確認可能。
加工方法 | 推奨板厚範囲 (mm) | 特徴 | メリット例 |
---|---|---|---|
レーザー切断 | 0.5~6.0 | 高精度で複雑な形状に対応可能 | 高いデザイン性と加工速度 |
プレス加工 | 0.5~3.0 | シンプルな形状に適した大量生産向け | 生産効率の向上 |
溶接 | 1.0~5.0 | 強度が必要な部位の接合に最適 | 一体感のある構造の実現 |
曲げ加工 | 0.5~4.0 | 複雑な立体形状の作成が可能 | 軽量で耐久性のある製品を実現可能 |
ステンレス板厚に関する最新技術動向
- 高強度薄板の活用
新合金技術により、従来よりも薄い板で高い強度を実現可能に。この技術を用いることで、軽量化とコスト削減を両立。 - デジタルシミュレーションの活用
最新のCAEソフトウェアにより、設計段階で板厚の最適化をシミュレーション可能。無駄を省き、コストと性能のバランスを事前に評価。
追加の提案:業者選びのポイント
業者選定の際、以下の3点を確認することが重要。
- 加工実績:類似製品の製造実績を持つ業者を選定
- 設備環境:最新の加工設備が揃っているかを確認
- 対応力:特殊仕様への柔軟な対応力があるか
まとめ
ステンレス板金の板厚選定は、コスト、性能、耐久性のバランスを取るための要。最新技術や適切な業者選びを活用し、最適な設計を追求することが重要。
ステンレス板厚選定で失敗しないための事例解説
実際の現場で発生した失敗例とその改善策を解説することで、具体的な知見を共有。
失敗例1: 板厚の過剰選定によるコスト増加
ある厨房機器メーカーが、耐久性を重視しすぎて必要以上に厚い板材を採用。結果として製品重量が増加し、運搬コストや取り扱い性が悪化。
改善策: 板厚を1mm減らすことで、材料費が10%削減されただけでなく、加工時間も短縮。CAE解析により、設計強度を確保しつつ、最適な板厚を選定。
失敗例2: 薄すぎる板材の選定による強度不足
建築材料において軽量化を優先しすぎ、使用した1mm厚の板材が長期間の風雨で変形。製品寿命が短縮し、顧客クレームが発生。
改善策: 部分的に補強材を追加することで、板厚を変更せず強度を向上。コスト増加を最小限に抑えながら、性能を改善。
ステンレス板厚と仕上げ加工の関係性
仕上げ加工の種類によって適切な板厚が異なるため、用途に応じた選定が重要。
各仕上げ加工に適した板厚と用途
仕上げ加工 | 推奨板厚範囲 (mm) | 主な用途 | 特徴 |
---|---|---|---|
ヘアライン加工 | 0.8~3.0 | 建築用パネル、装飾品 | 美しい光沢と耐傷性を実現 |
ミラー仕上げ | 1.0~2.0 | 高級家具、内装パネル | 高級感を演出し、清掃性も良い |
サンドブラスト加工 | 0.8~4.0 | 屋外装飾、工業部品 | 滑り止め効果や独特のデザイン性を提供 |
酸洗仕上げ | 1.0~6.0 | 医療機器、食品加工設備 | 表面の不純物を除去し、清潔性向上 |
ステンレス板厚の最適化に役立つ最新ツール
板厚選定の効率化には、最新技術を活用することで精度とスピードが向上。
最新ツール一覧
- CAE解析ソフト
- 板厚による強度シミュレーションを迅速に行える。ANSYSやSolidWorksなどが代表例。
- 導入事例: 精密機械メーカーがCAEを活用し、板厚削減で年間コストを15%削減。
- AIによる最適化ツール
- AIアルゴリズムを活用し、最小板厚で必要性能を満たす設計を自動提案。
- 導入事例: 自動車メーカーがAIツールを使用し、製造過程での材料ロスを大幅に削減。
- デジタルツイン技術
- 製造前に仮想環境で板厚や加工の影響を確認。生産の失敗リスクを削減可能。
- 導入事例: 航空部品メーカーがデジタルツインを活用し、試作コストを30%削減。
板厚と業者選びの見落としがちなポイント
業者選びでは、以下のポイントを見落とすと大きなリスクを伴う。
ポイント1: 加工の専門性
すべての業者が、複雑な形状や薄い板材の加工に対応できるわけではない。
例: 特殊な曲げ加工に強みを持つ業者を選ぶことで、設計精度を向上し、品質を確保。
ポイント2: 使用機材の最新性
古い設備では加工精度や対応可能な板厚に限界がある。最新機材を持つ業者では、コスト削減と品質向上が期待できる。
ポイント3: 納期対応力
緊急納品が必要なプロジェクトでは、迅速な対応が可能な業者を選ぶべき。過去の納期実績を確認することが推奨される。
まとめ
ステンレス板厚選定は、製品の性能やコストに直結する重要なプロセス。
失敗例や成功事例、最新技術を活用した最適化方法を理解し、さらに業者選びにおいて正しい判断を下すことが、長期的なコスト削減と製品品質向上の鍵となる。